In the rapidly evolving electronics industry of the new era, products are increasingly becoming smaller, lighter, multi - functional, and highly integrated. Precision injection molding, a crucial process for manufacturing electronic components, relies on mold design precision and quality to determine the quality of injection - molded products. High - precision mold design ensures dimensional accuracy and appearance quality of electronic products and significantly impacts production efficiency and cost control.
Molds in the electronics field endure repeated injection pressure, temperature changes, and friction. Thus, high - strength, high - hardness, and wear - resistant mold steel is preferred. For example, Cr12MoV steel, after quenching and tempering, reaches a hardness of HRC58 - 62. It can withstand frequent mold opening/closing and plastic melt erosion during electronic injection, maintaining good dimensional accuracy over long - term use.
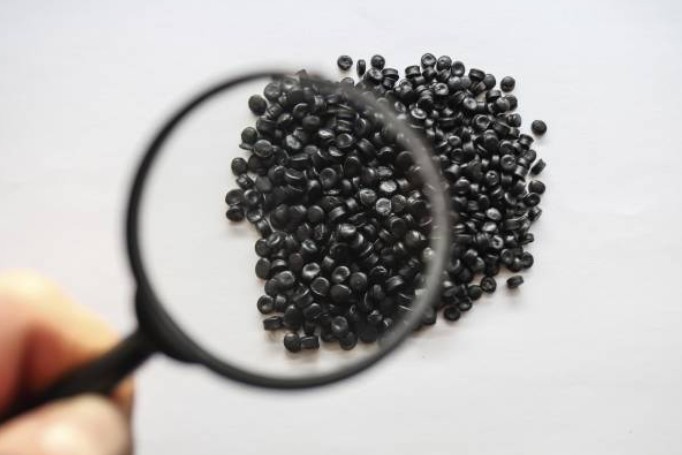
During electronic product injection, rapid temperature changes occur. Mold materials need excellent thermal stability and thermal conductivity. H13 steel has outstanding thermal fatigue resistance, reducing thermal cracking under frequent cold - hot cycles and ensuring mold service life. Its good thermal conductivity also enables rapid mold cooling, shortening cycle times and boosting productivity.
Electronic components demand high - quality surfaces. Impurities and pores in mold materials can cause defects like air holes and pits in injection - molded parts. Thus, high - purity mold steel is used. Advanced smelting processes such as electro - slag remelting reduce harmful impurities and gases, enhancing mold surface quality.
The parting surface affects mold opening, part demolding, and molding quality. For precision electronic injection molds, it should be at the part's maximum contour for easy demolding. Also, consider the part's appearance to avoid parting lines on visible surfaces. For complex - appearance products like mobile phone casings, a hidden parting surface (e.g., at edges or bottom) can be used.
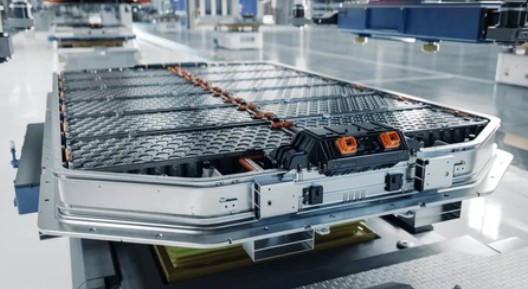
The gating system must ensure rapid and uniform plastic melt filling. The diameter and length of the sprue and runner are designed based on part size, weight, and plastic fluidity. In electronic injection, hot - runner systems are often used. They keep the melt molten at high temperatures, reducing pressure loss, improving injection efficiency, and avoiding gate marks for better part appearance.
The cooling system is key to ensuring part dimensional accuracy and shortening cycle times. For precision electronic injection molds, cooling channels are arranged according to part shape and size. Conformal cooling (designing channels to follow the part contour) ensures uniform cooling, reducing part deformation. Efficient coolants like low - temperature water or cooling fluids enhance cooling efficiency.
The ejection mechanism must enable smooth part demolding without damaging surface or dimensional accuracy. For precision electronic parts, ejection pins, ejector plates, or slides are used. Ejection components' positions are rationally arranged to avoid marks. For parts with undercuts (e.g., electronic connectors), side core - pulling mechanisms (slides or angle lifters) are designed for smooth demolding.
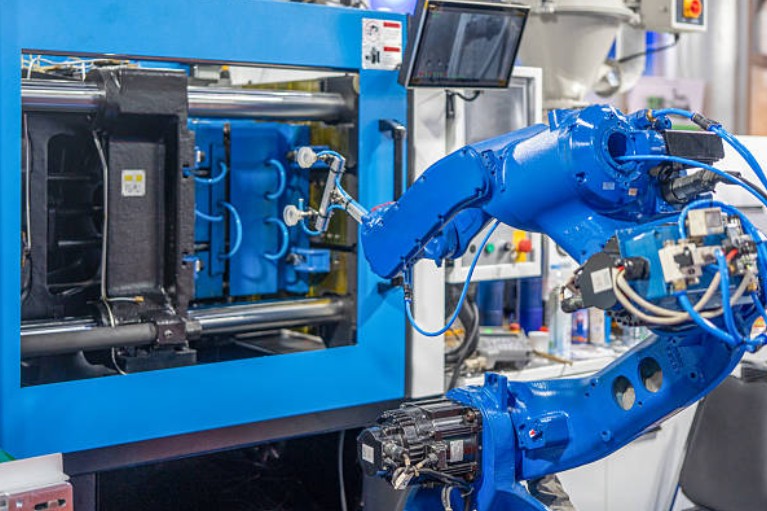
Electronic parts require high dimensional accuracy. Mold design strictly controls tolerances. Based on part function and assembly requirements, mold part manufacturing tolerances are rationally allocated, usually 1/3 - 1/5 of the part tolerance. For example, for a part with a ±0.05mm tolerance, mold part manufacturing tolerance may be ±0.01 - ±0.015mm.
Plastics shrink during injection. Different materials and molding conditions cause varying shrinkage. Mold design requires accurate shrinkage data (from tests or suppliers). Combined with mold structure and process, cavity and core dimensions are adjusted to ensure part dimensional accuracy.
万彩网100线路Mold part fit precision impacts part dimensional accuracy. Rational fit clearances (e.g., between slides and channels, ejection pins and holes) are ensured. High - precision machining (e.g., wire - cutting for slides and channels with ±0.005mm clearance) guarantees smooth and accurate movement.
CAD enables 3D mold modeling, structural optimization, and interference checking, improving design efficiency. CAE simulates injection molding, predicting melt flow, temperature/pressure distribution, and part shrinkage/deformation. It helps identify design issues early, optimizing mold structure and process parameters for higher success rates.

3D printing (additive manufacturing) plays an increasing role in mold design. For molds with complex cooling channels or special structures, 3D printing directly manufactures mold parts. It shortens manufacturing cycles and enables structures hard to achieve with traditional methods, enhancing mold performance and efficiency.
In the new era, intelligent manufacturing and information management are applied to mold design. Digital workshops enable automated, intelligent mold manufacturing. Sensors and monitoring systems collect data (e.g., processing parameters, equipment status). Data analysis optimizes manufacturing, ensuring high precision and quality.
High - precision mold design for electronic - field precision injection molding is a complex, systematic project involving material selection, structure design, dimension control, and new - era technology application. With the electronics industry's development and technological progress, mold design requirements will keep rising. Designers must continuously learn new technologies and concepts to improve design levels, providing high - quality, efficient mold solutions for the electronics industry.
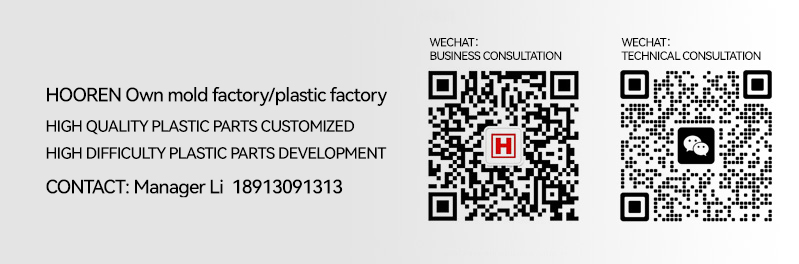