Precision Injection Molding: Key Processes and Technical Specifications
2025-06-16 10:51:04
Precision Injection Molding
Material Selection
Engineering plastics for precision molding require high mechanical strength, dimensional stability, creep resistance, and environmental stress cracking resistance. Common materials include:
万彩网100线路Polycarbonate (PC): Applied in optical lenses and electronic enclosures for its transparency, heat resistance, and dimensional stability.
万彩网100线路Polyoxymethylene (POM): Suitable for precision gears and mechanical parts, featuring high rigidity, low friction, and fatigue resistance.
Drying Treatment
Moisture in plastic pellets can cause surface defects like silver streaks and bubbles, and reduce mechanical properties. For hygroscopic materials such as Nylon (PA), drying parameters are critical:
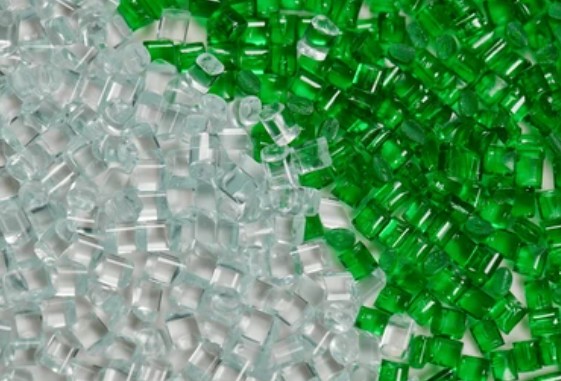
Mold Precision Design
Cavity dimensions are calculated based on shrinkage rates, influenced by:
万彩网100线路Gate type, location, and distribution
Material crystallization orientation (anisotropy)
万彩网100线路Part geometry, size, and distance from the gate
Tolerance: ≤±0.005 mm
万彩网100线路Surface roughness: Ra 0.1–0.05 μm
Gate Design
万彩网100线路Pin-point gate: For high-precision parts with minimal gate marks.
Edge gate: Versatile for various shapes, requiring careful placement to avoid weld lines.
万彩网100线路Submarine gate: Hidden within the mold, suitable for aesthetic components.
Cooling System Design
万彩网100线路Maintain uniform mold temperature (±1°C variation) to minimize shrinkage and warpage.
万彩网100线路Use circulating water channels around the cavity.
万彩网100线路For complex molds, adopt zone-controlled cooling for uneven heat distribution.
Mold Manufacturing Processes
Electrical Discharge Machining (EDM): Achieves ±0.01 mm precision for complex shapes.
万彩网100线路Wire-cut EDM: Cuts intricate features with ±0.005 mm accuracy.
万彩网100线路Grinding: Ensures surface flatness within ±0.002 mm.
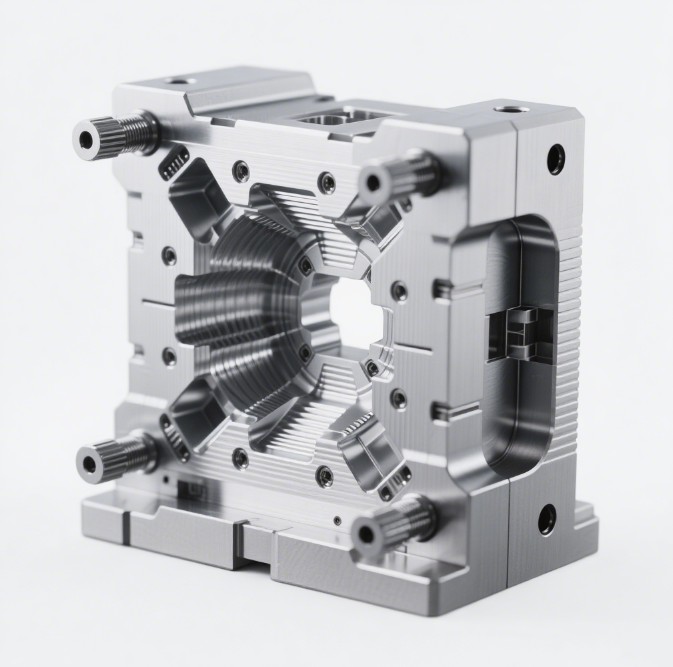
Injection Speed
Apply segmented injection for complex molds:
Stage 1: Slow filling (30% speed, 40 bar) to avoid jetting.
Stage 2: Medium speed for intricate sections.
Stage 3: Fast filling to 95% of cavity volume.
Stage 4: Slow buffer for packing.
Packing Pressure and Time
Injection Pressure
Barrel Temperature
PP: 180–230°C
PC: 270–320°C
Mold Temperature
Crystalline plastics (e.g., PE, PP): Higher temperatures for uniform crystallization.
Amorphous plastics (e.g., PS, PMMA): Optimized for flow and surface finish.
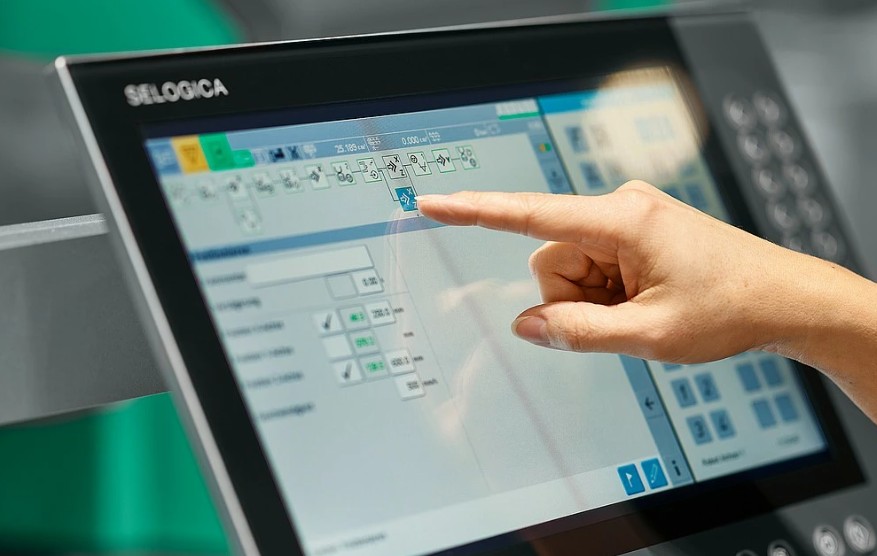
Injection System Precision
Screw diameter and L/D ratio tailored to part size.
Shot volume accuracy: ≤±0.5%.
Pressure control: ≤±1 MPa fluctuation.
Clamping System Rigidity
Control System Stability
Digital control with real-time monitoring of speed, pressure, and temperature.
Fault diagnosis and alarm functions.
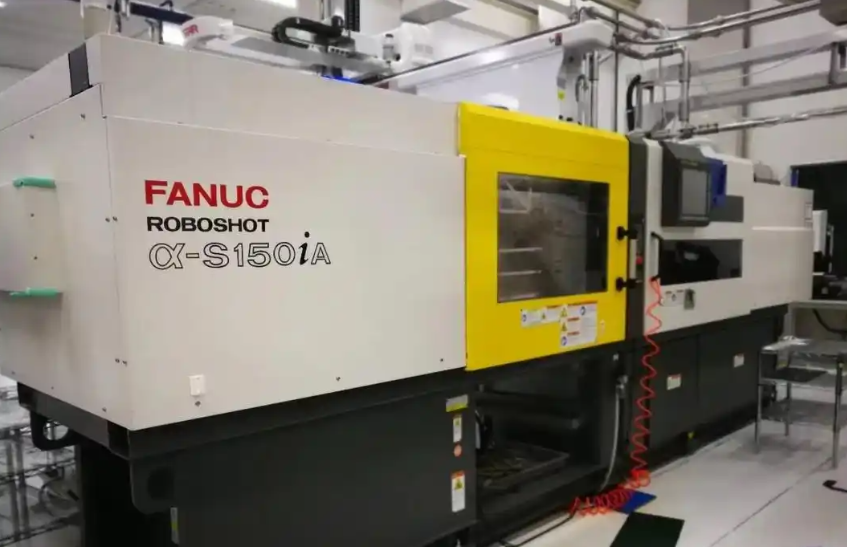
Annealing
Moisture Conditioning
Surface Treatment
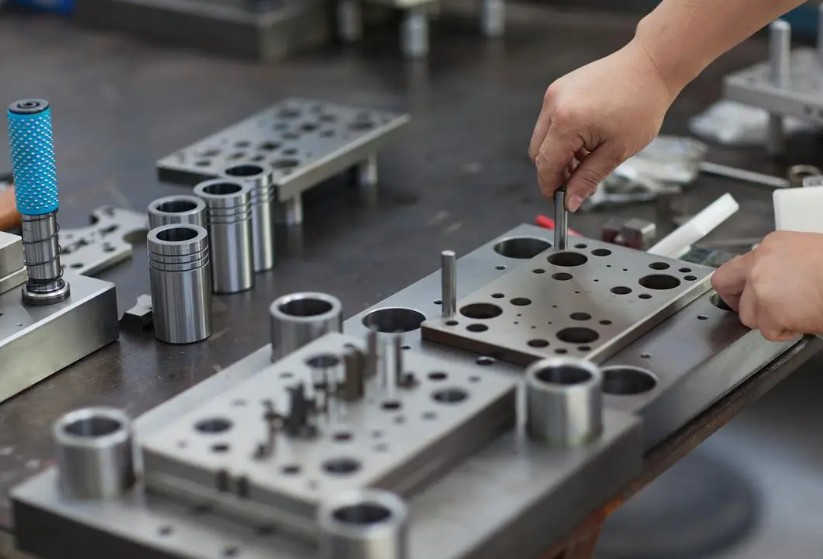
Conclusion
Precision injection molding requires strict control across material selection, mold design, process parameters, equipment, and post-processing. Optimizing each stage ensures dimensional accuracy, surface quality, and mechanical performance for high-value applications.
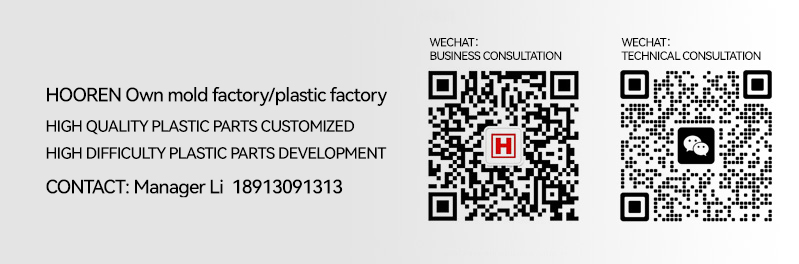