Injection molding is a prevalent plastic processing method. However, flash frequently occurs during injection molding, marring product appearance, compromising dimensional accuracy, and escalating post - processing costs. Addressing this issue is essential for enhancing product quality and production efficiency.
High injection pressure万彩网100线路: Excessive pressure forces melt to overflow from mold gaps when cavity pressure surpasses clamping force.
Fast injection speed: Rapid filling creates high - pressure zones in weak mold areas, leading to flash.
Overlong/strong holding pressure: Excessive holding pressure or time squeezes too much melt into the cavity, increasing flash risk.
High barrel temperature: Lowered melt viscosity due to high heat makes it prone to overflow.
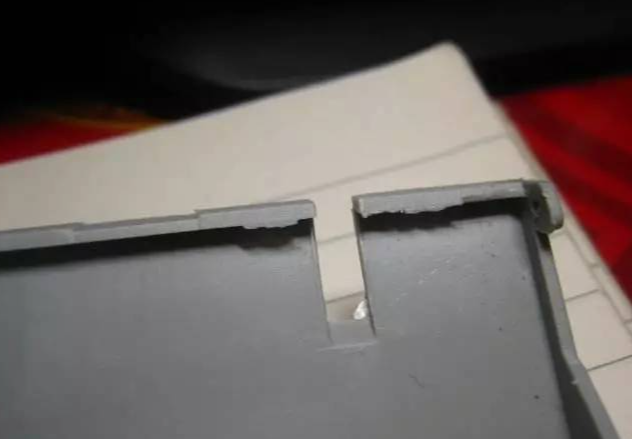
Uneven parting surface: Poor machining of the parting surface prevents tight mold closure, causing flash.
Large mold clearances: Excessive gaps between components like sliders and chutes, or ejector pins and holes, allow melt leakage.
Weak mold structure万彩网100线路: Inadequate mold strength from improper design or material selection causes deformation and flash under pressure.
Variable fluidity: Different plastic batches or brands with high fluidity are more likely to cause flash.
Impurities万彩网100线路: Contaminants in plastic alter its properties, triggering local abnormal flow and flash.
Low clamping force: Insufficient clamping force fails to counteract mold expansion, opening the parting surface.
Poor template parallelism万彩网100线路: Uneven clamping due to misaligned templates creates large gaps and flash.
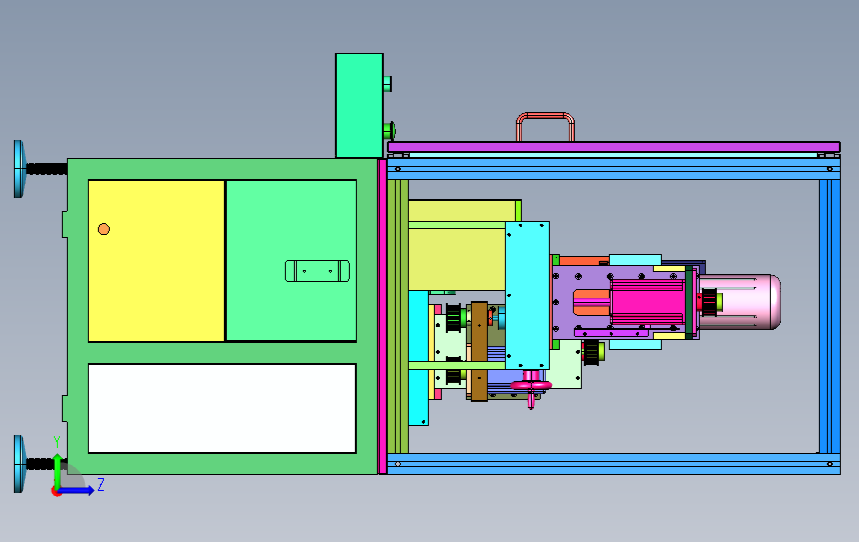
Adjust pressure: Gradually lower injection pressure and use multi - stage injection.
Control speed万彩网100线路: Adapt speed to product shape; use slow - fast - slow curves for complex items.
Fine - tune holding pressure万彩网100线路: Determine optimal holding pressure and time through trials.
Regulate temperature万彩网100线路: Set barrel temperature to balance plasticization and viscosity.
Enhance parting surface万彩网100线路: Use high - precision machining; grind or polish worn surfaces.
Reduce clearances: Control component clearances; repair large gaps with inserts or electroplating.
Strengthen mold万彩网100线路: Optimize design, select suitable materials, and add reinforcing structures.
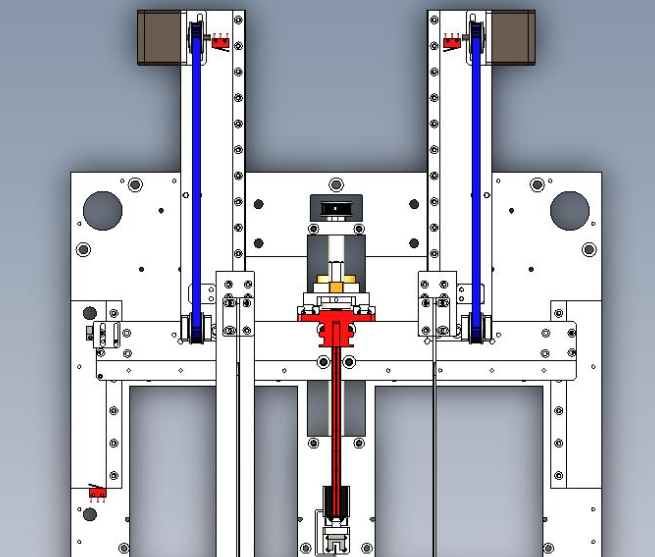
Case 1 (Electronics): High injection pressure, long holding time, and a worn parting surface caused flash. Reducing pressure, shortening holding time, and repairing the surface resolved the issue.
Case 2 (Automotive)万彩网100线路: Large ejector - pin gaps and misaligned templates led to flash. Re - machining components and correcting the template improved the situation.
Flash in injection - molded products stems from multiple factors. Solutions require a comprehensive approach, covering process parameter adjustment, mold improvement, raw material management, and equipment maintenance. Continuous monitoring and optimization in production can boost product quality and efficiency.
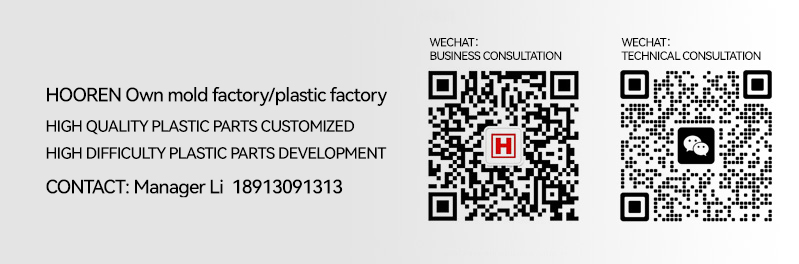